Ceramic glazes are a type of glass that is applied to the surface of ceramics to give them a smooth, glossy finish.
Glazes can also be used to add color or decoration to ceramics.
In this blog post, we'll take a closer look at what ceramic glazes are, how they're made, and some of the most popular types of glazes used by artists today.
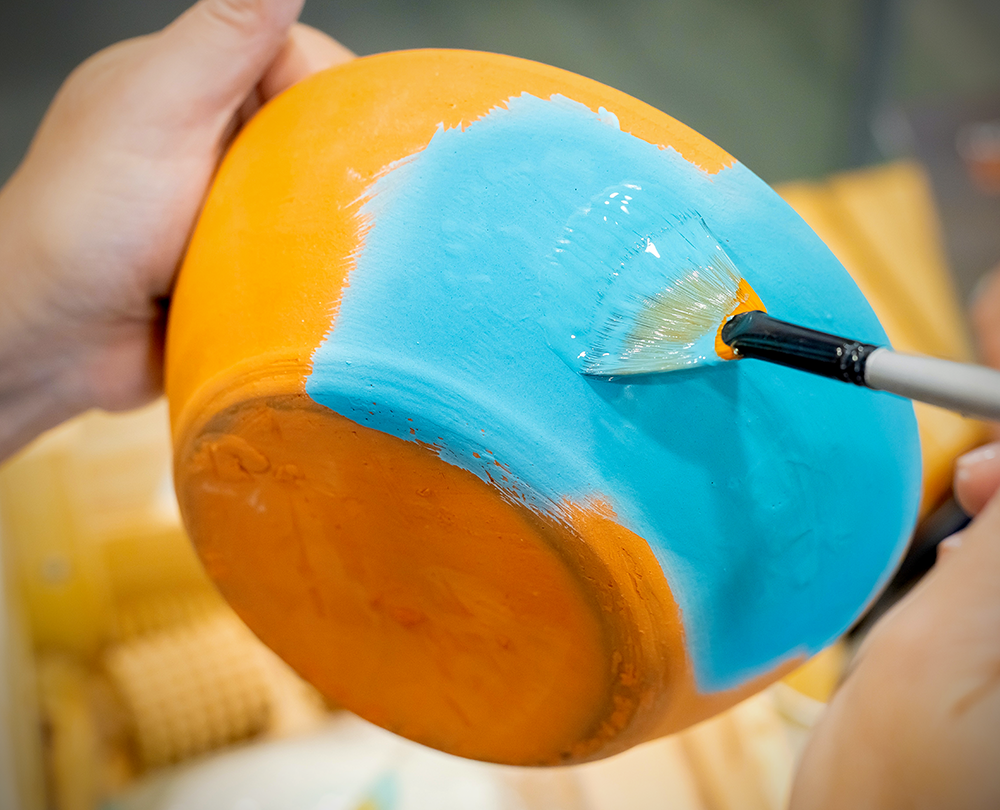
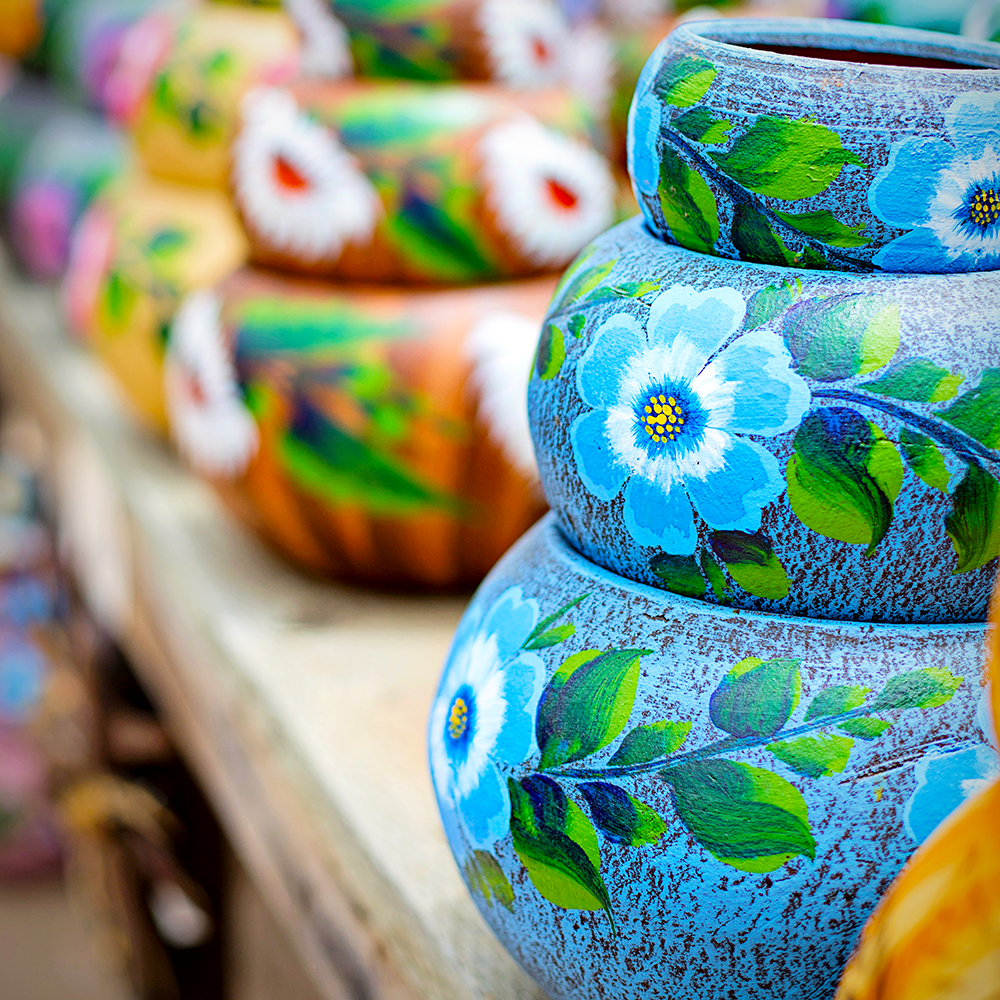
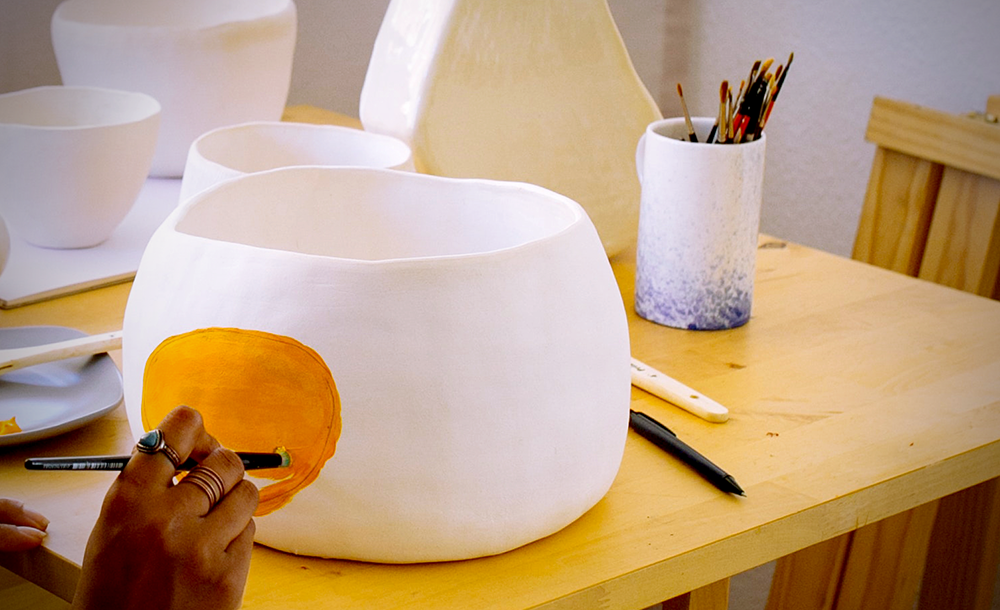
What Is Ceramic Glaze?
Ceramic glazes are a type of glass that is melted and then applied to the surface of ceramics.
These glazes are made from a mixture of minerals and other materials that are melted together at high temperatures.
The most common type of ceramic glaze is made from feldspar, silica, and kaolin clay.
Other materials that can be added to ceramic glazes include metals, oxides, and colorants.
The word "glaze" comes from the Old English word "glæs," which means "glass."
They come in many types, including lead-free glaze, luster glaze, dipping glaze, crackle glazes, and many more.
When glaze is applied to the surface of ceramics, it gives the piece a smooth, glossy finish whiling adding color or decoration to ceramic pieces.
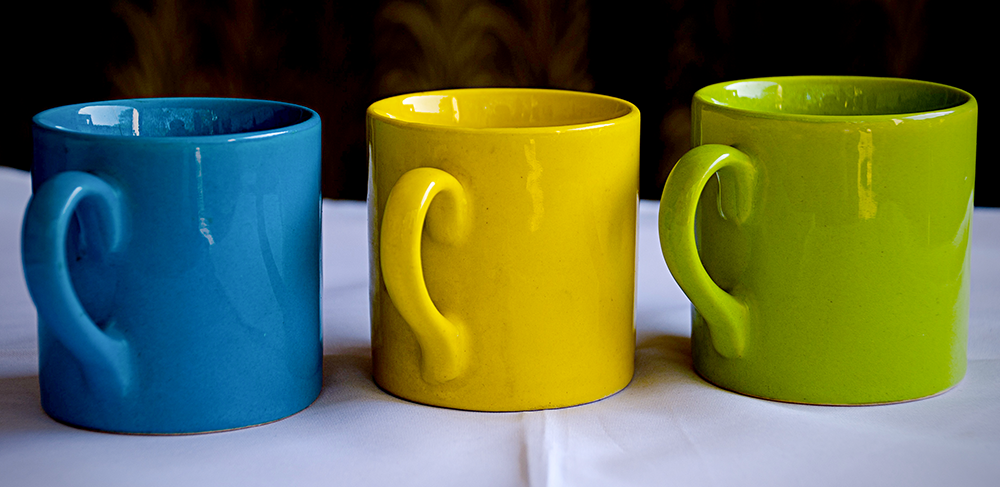
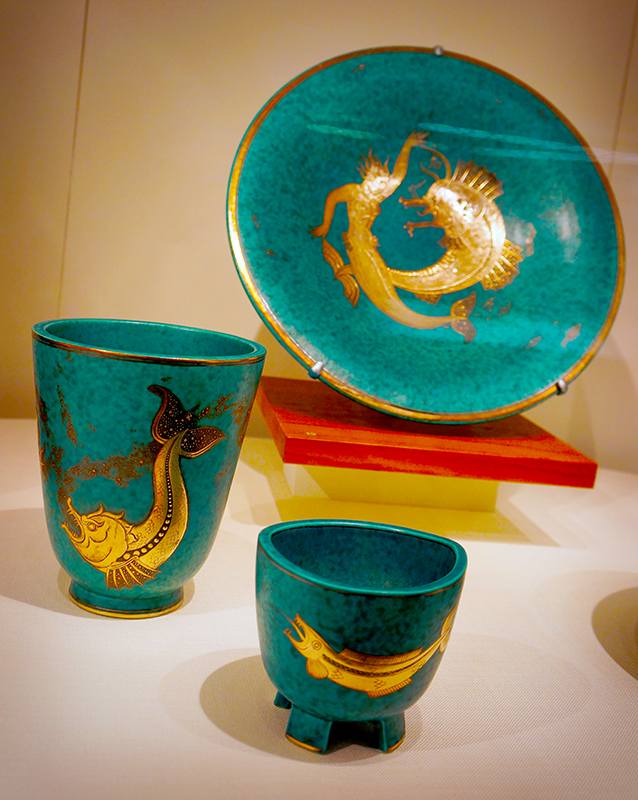
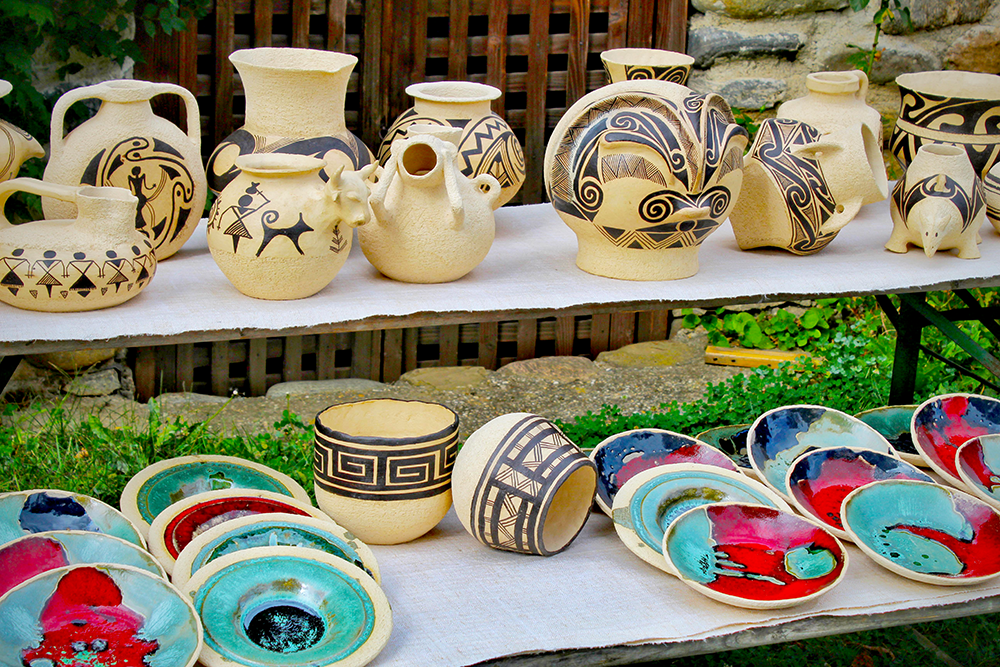
How Is Ceramic Glaze Made?
Ceramic glaze is made from a mixture of materials including silica, alumina, and fluxes.
These materials are melted together in a kiln at temperatures between 2200°F and 3000°F.
Once the materials have melted, they are poured into molds or applied to the surface of ceramics.
After the glaze has cooled, it becomes hard and glossy.
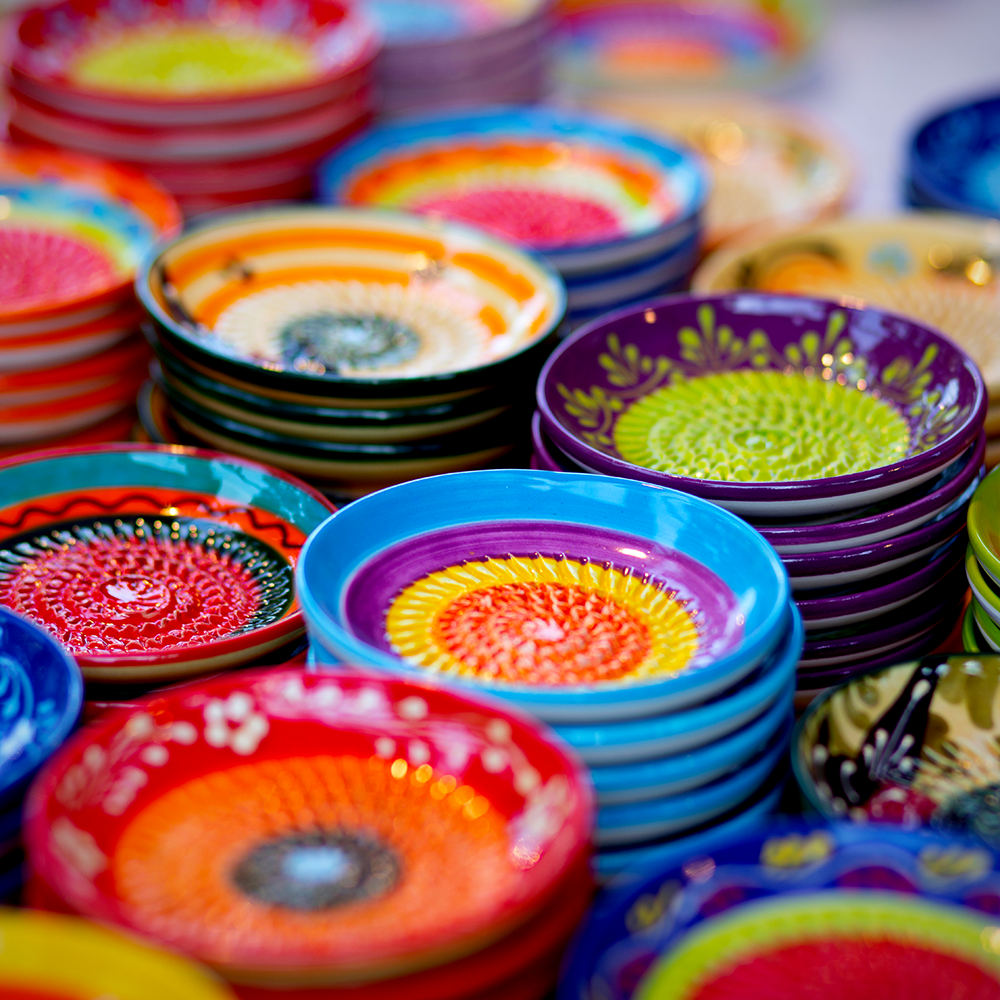
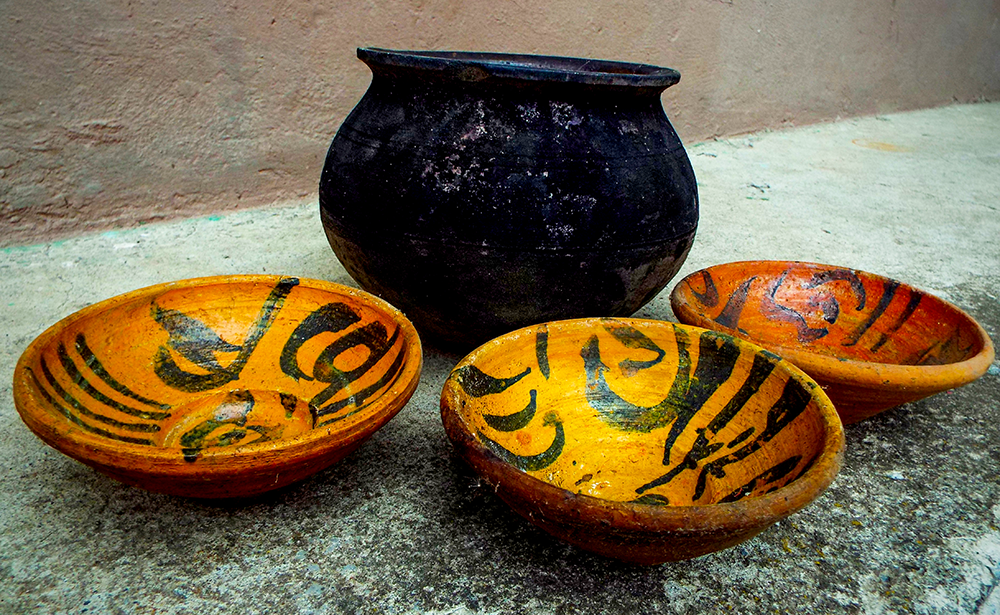
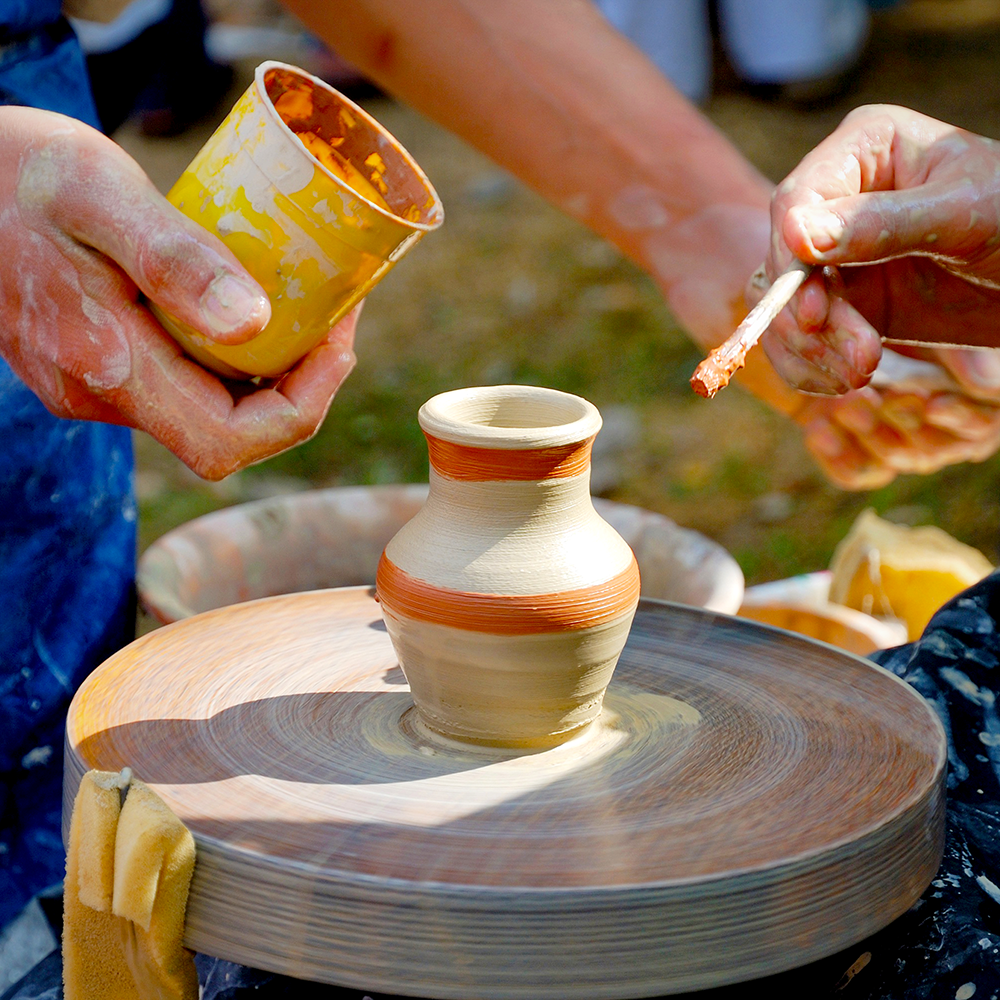
Different Types of Ceramic Glazes
There are many different types of ceramic glazes available on the market today.
Some of the most popular types of glazes include:
- Clear glazes: Clear glazes are transparent and allow the color of the clay body to show through. They are typically used on functional pieces such as plates and cups.
- Opaque glazes: Opaque glazes are non-transparent and do not allow the color of the clay body to show through. They come in a wide range of colors including white, black, blue, and green.
- Metallic glazes: Metallic glazes contain finely ground metals such as copper or bronze that give them a shimmery appearance. They are often used for decorative purposes.
- Crystalline glazes: Crystalline glazes contain materials that cause them to form crystals as they cool. They come in a wide range of colors and patterns and can be used for both functional and decorative pieces.
- Underglaze: Underglaze is a type of glaze that is applied to the surface of ceramics before the piece is fired. It is typically used to add color or decoration to the piece.
- Overglaze: Overglaze is a type of glaze that is applied to the surface of ceramics after the piece is fired. It is typically used to add color or decoration to the piece.
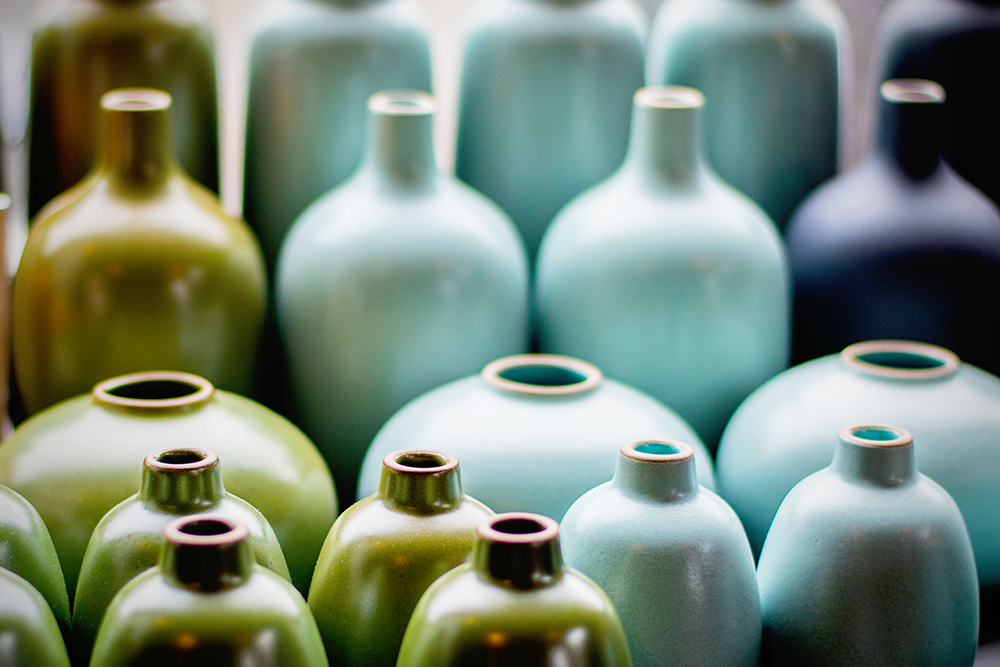
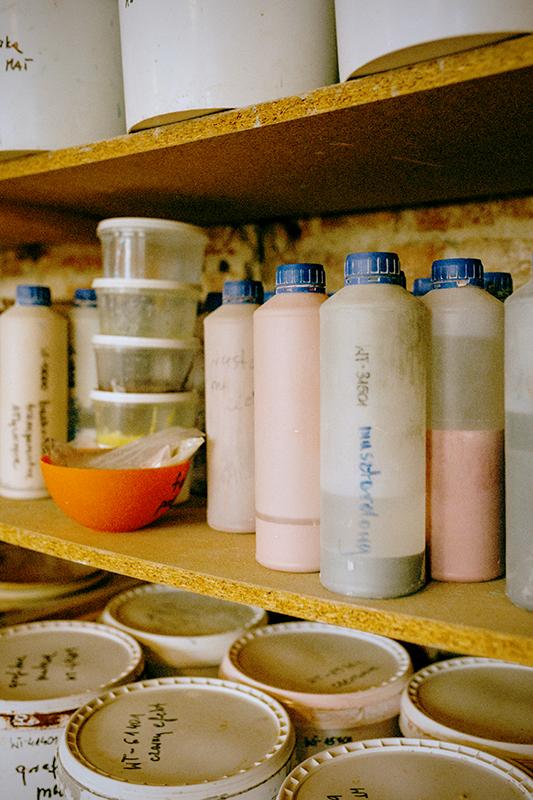
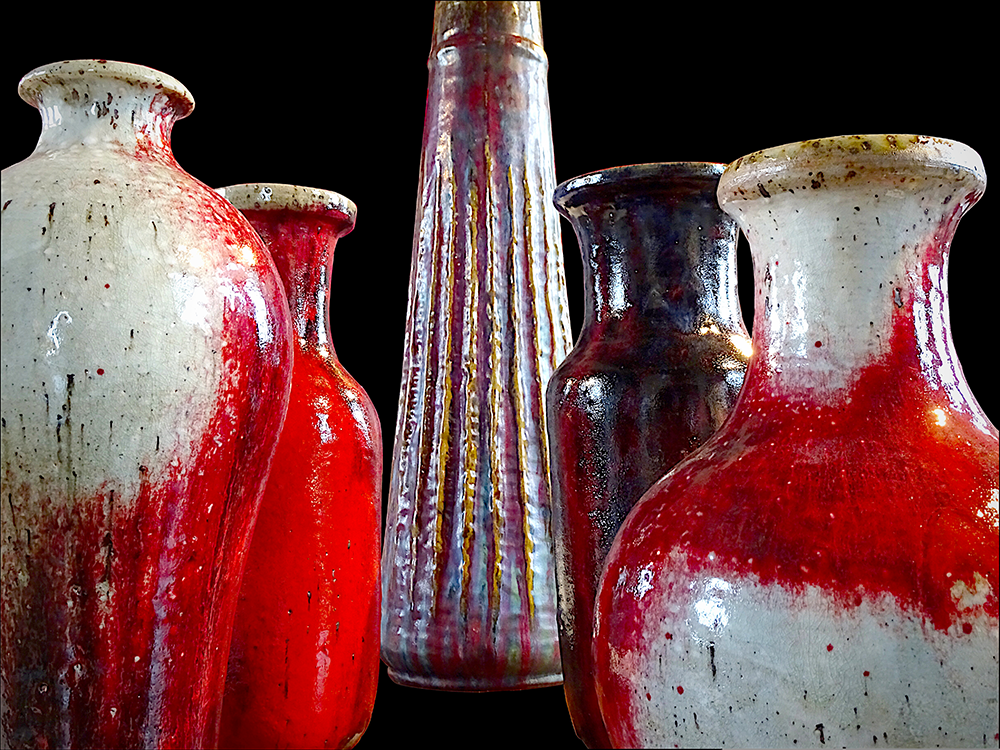
Glazing Pottery
Applying pottery glazes to ceramics is a fairly simple process.
First, the piece of ceramic ware is cleaned and bisque fired (most glazes require a pieces to be bisque ware prior to application, aside from ones like underglazes).
Next, the liquid glaze is mixed and applied to the surface of the piece using a brush or sponge.
Some glazes are dipping glazes, which means they are applied by dipping the piece of ceramic ware into a bucket of glaze.
Once the glaze is applied, it is allowed to dry.
You can also create wax resist designs on the surface of the glaze before it dries.
After the wax resist design is created, the piece is then dipped into the glaze or applied with a paint brush.
The wax resist will prevent the glaze from adhering to the waxed areas, creating a design on the surface of the glaze.
After the glaze is dry, the piece is fired in a kiln at high temperatures (usually between 1200°F and 1400°F).
This firing process melts the glaze, causing it to flow and form a smooth, glossy finish.
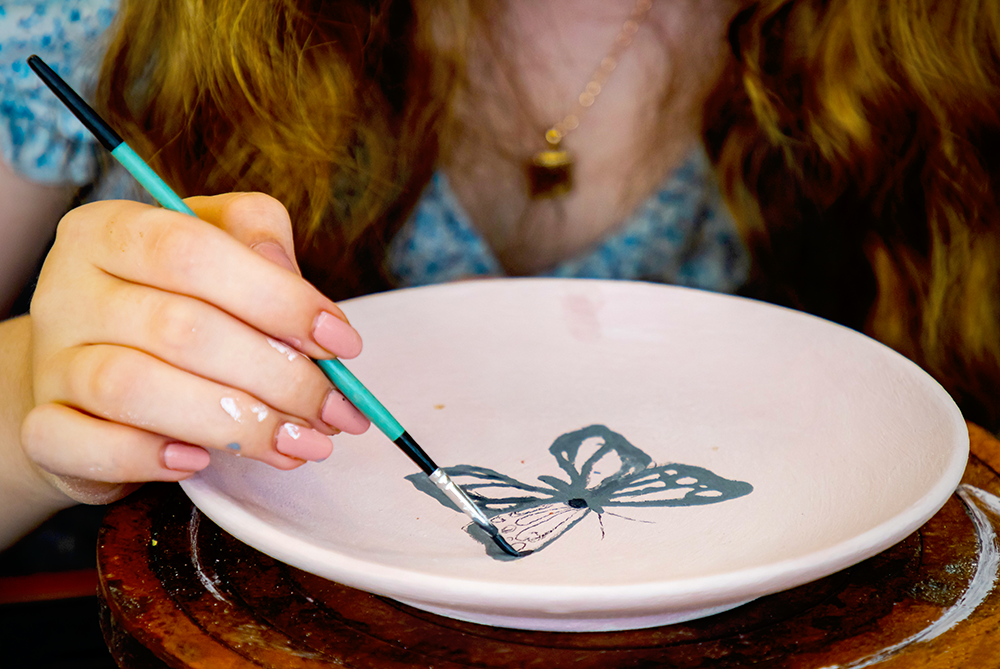
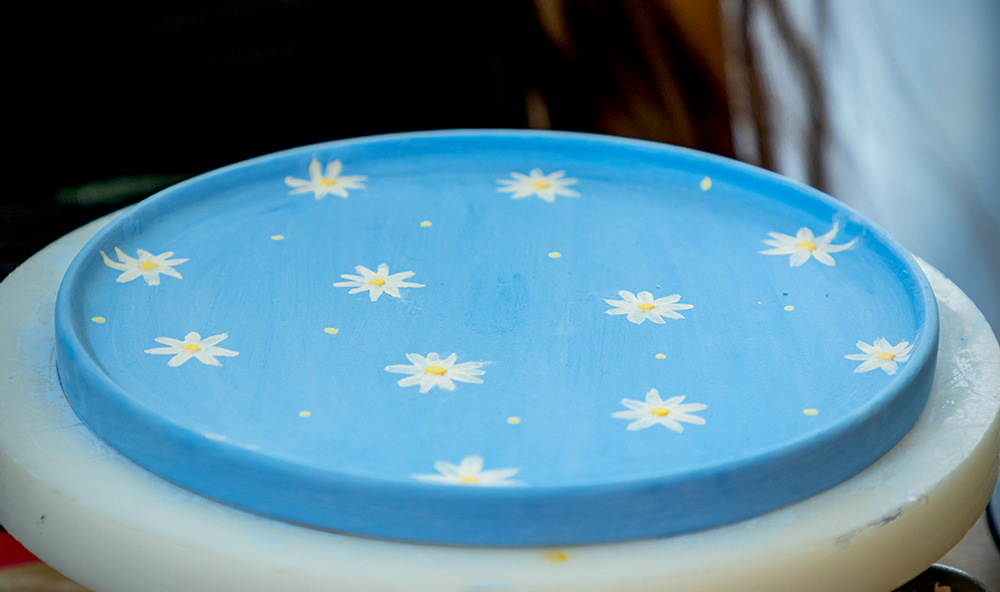
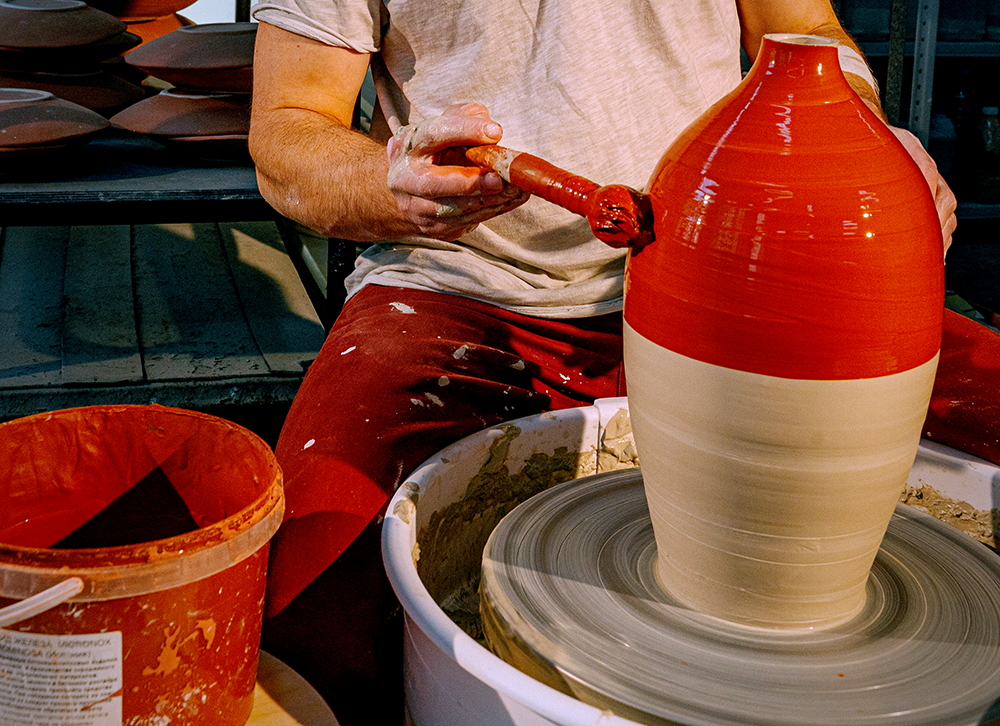
Different Types of Fired Glaze
Pottery glaze requires different kinds of firing; there are high-fire, mid-fire, and low fire glaze, so be sure you're using the right type of glaze for your project.
High-fire glazes are fired at temperatures between 2200°F and 3000°F.
Mid-fire glazes are fired at temperatures between 1800°F and 2200°F.
Low-fire glazes are fired at temperatures between 1200°F and 1800°F.
Using the improper temperature when firing your glaze can cause it to craze (crackle), run, or become dull.
High-fire glaze should never be used on low-fire clay, as it will cause the clay to warp and crack.
Nor should low-fire glaze be used on high-fire clay, as it will not adhere properly and will cause the glaze to run.
It is important to follow the manufacturer's instructions when firing your glaze.
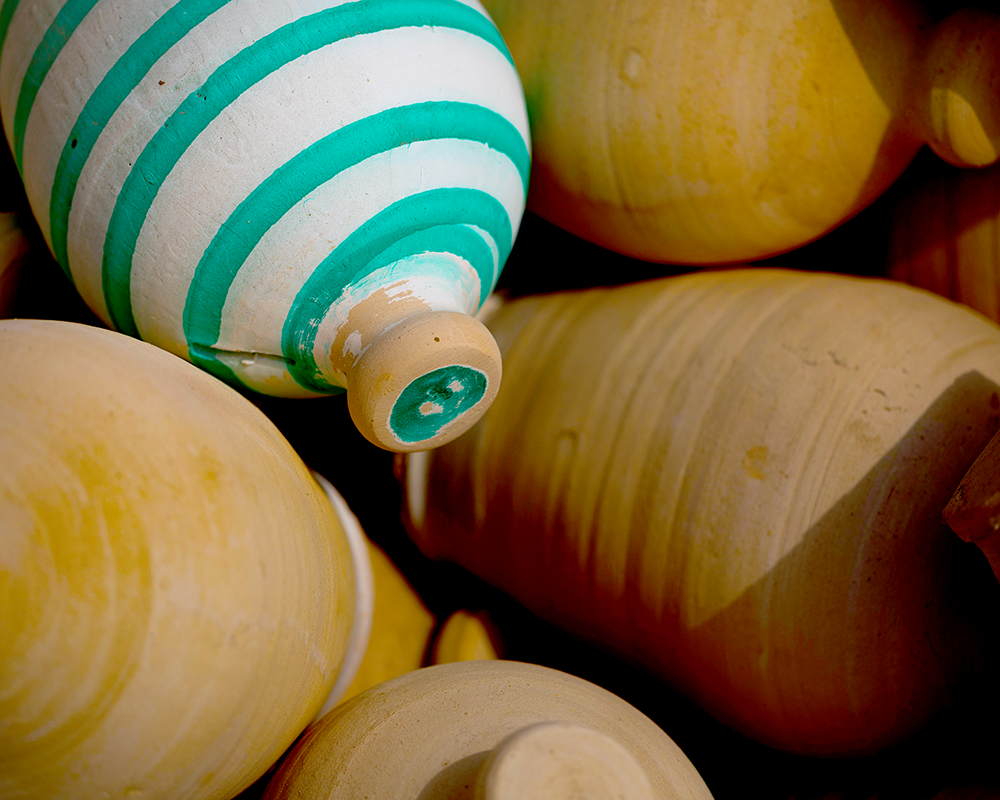
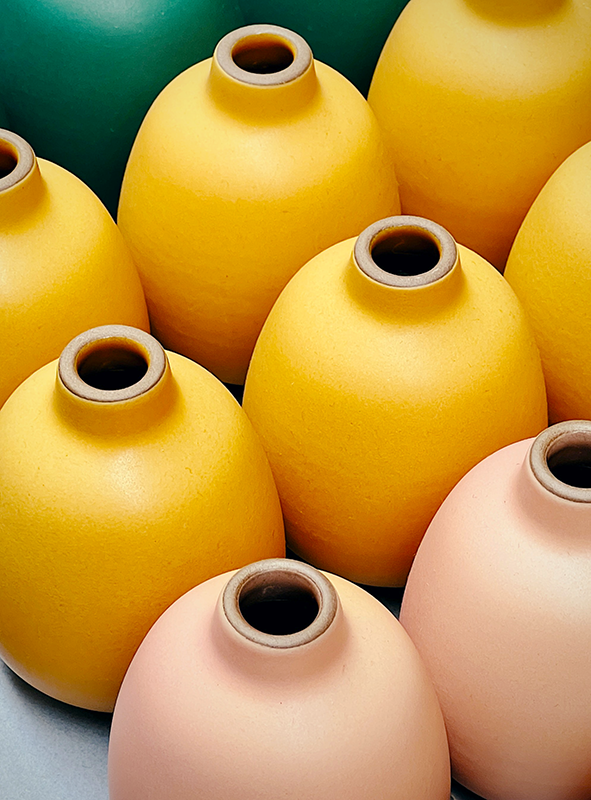
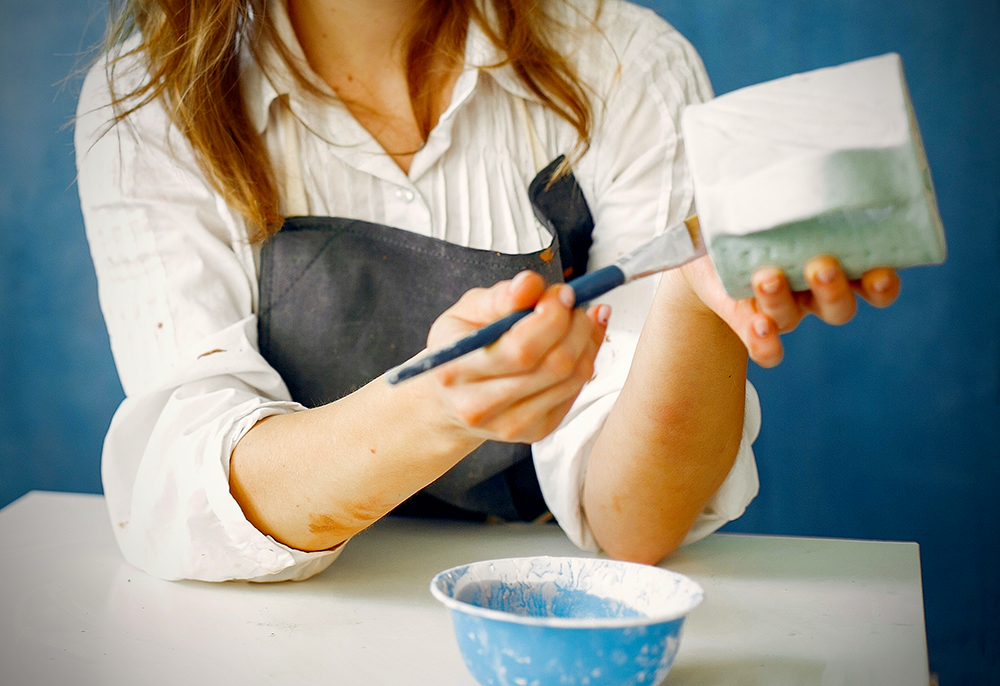
Different Types of Firing
There are two main kiln firing types that can be used to apply glazes to ceramics: electric and gas.
- Electric kilns: Electric kilns are the most common type of kilns used to fire glazes. They use electricity to heat the ceramic piece and are typically fired to temperatures between 1200°F and 1400°F.
- Gas kilns: Gas kilns use natural gas or propane to heat the ceramic piece and are typically fired to temperatures between 2200°F and 3000°F.
The type of firing and temperature requirements depend on the type of glaze and clay being used.
Some glazes require a higher firing temperature in order to melt and flow properly, while others can be fired at lower temperatures.
There are many ways you can glaze and fire your ceramics.
Soda ash firing is a type of gas firing that uses soda ash as the primary source of heat.
Soda ash firing is typically done in a kiln that is lined with bricks that have been soaked in soda ash.
The soda ash creates a chemical reaction with the glaze, resulting in a unique surface finish.
Raku firing is a type of low-temperature firing that is typically done in an electric kiln.
Raku firing is a quick process, typically taking less than an hour.
The piece is fired to a temperature between 1500°F and 1800°F and then removed from the kiln and placed into a container of combustible material such as newspaper or sawdust.
The container is then sealed and allowed to cool, resulting in a unique surface finish.
Pit firing is a type of low-temperature firing that is typically done in a pit dug into the ground.
The piece is placed into the pit and covered with combustible materials such as wood, straw, or leaves.
The pit is then sealed and allowed to cool, resulting in a unique surface finish.
Wood firing is a type of high-temperature firing that is typically done in a kiln that burns wood as its primary source of heat.
Wood firing is a long process, typically taking several days.
The piece is placed into the kiln and fired to a temperature between 2200°F and 3000°F.
The wood firing process creates a unique surface finish.
Glaze firing schedules and other firing process can be found in many ceramic books or online.
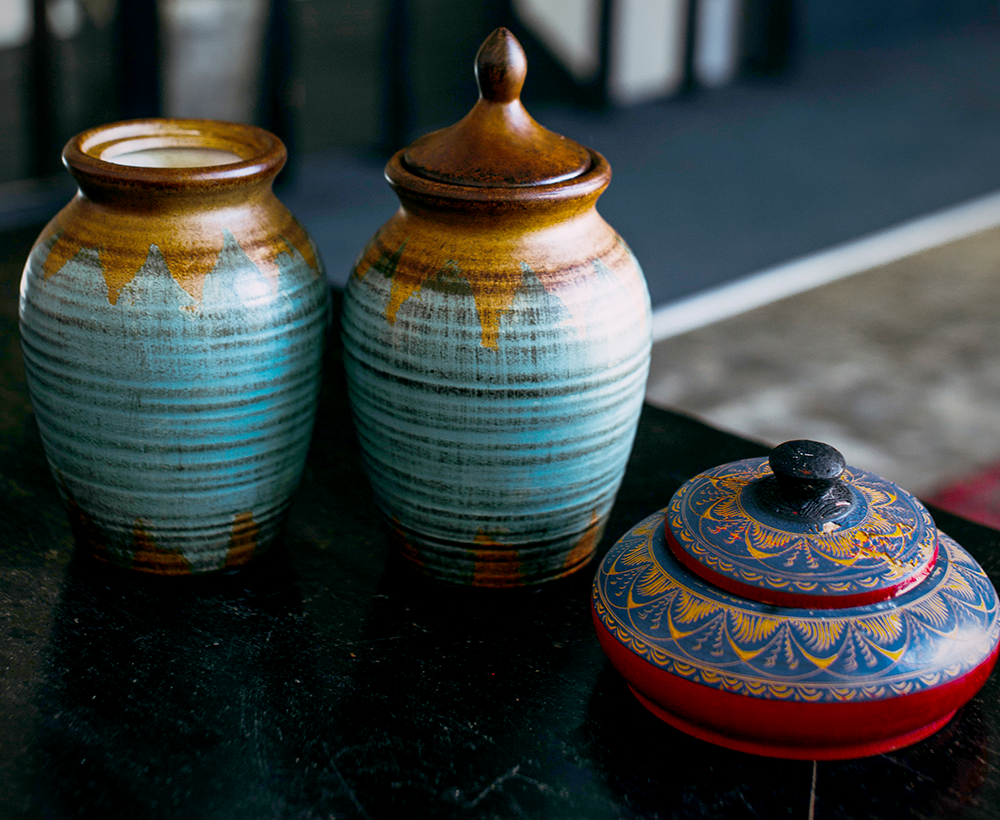

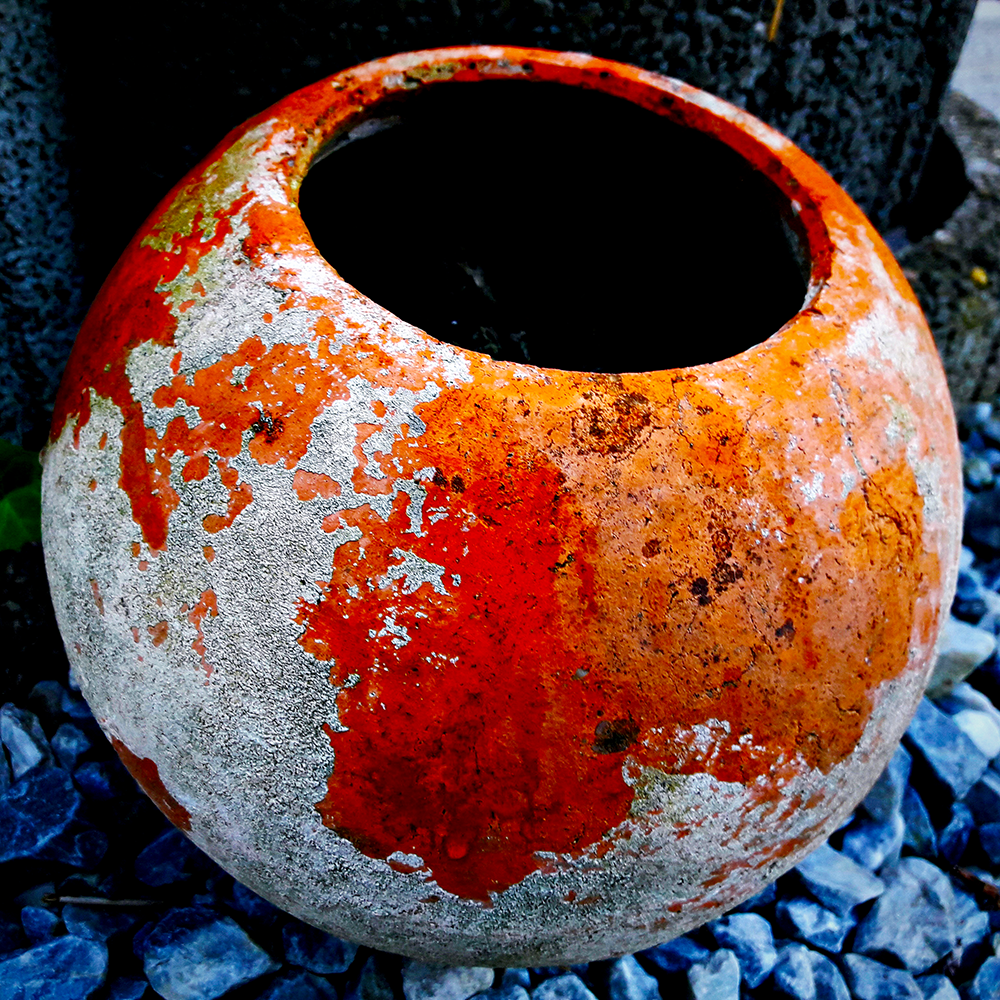
Glossy Glazes
There are many different types of glazes that can be applied to ceramics, each with its own unique finish.
The type of firing, temperature, and duration all play a role in the final appearance of the glaze.
Different types of clay and glazes require different firing schedules, so it is important to consult a ceramic book or online resource before beginning the firing process.
In this blog post, we've taken a closer look at what ceramic glazes are, how they're made, and some of the most popular types of glazes used by artists today.
Whether you're looking for a clear glaze for your next set of plates or a crystalline glaze for your next sculpture, there's sure to be a type of ceramic glaze that's perfect for your needs!
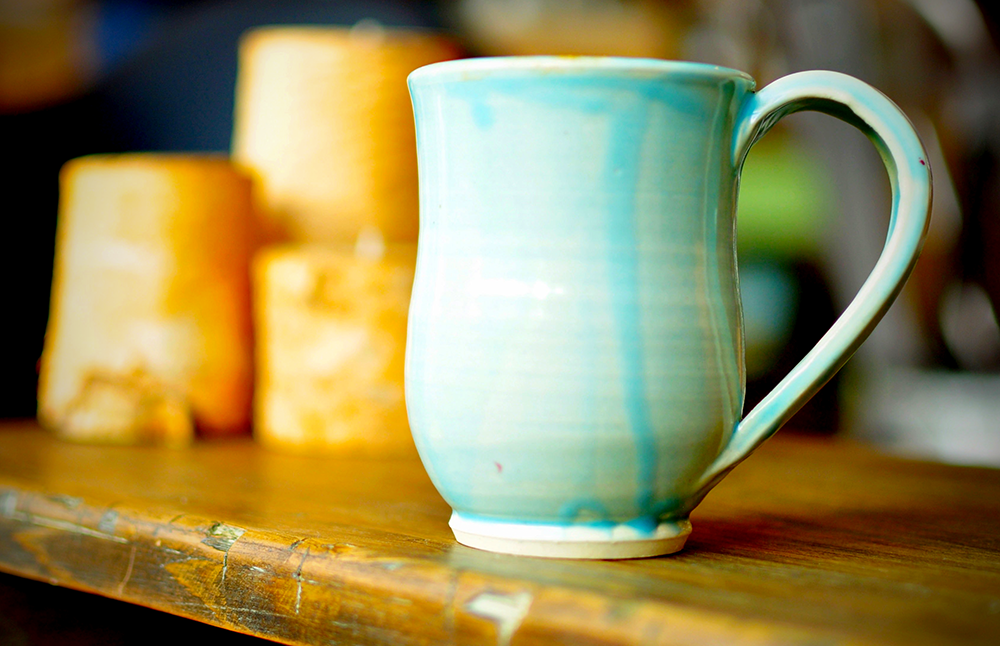
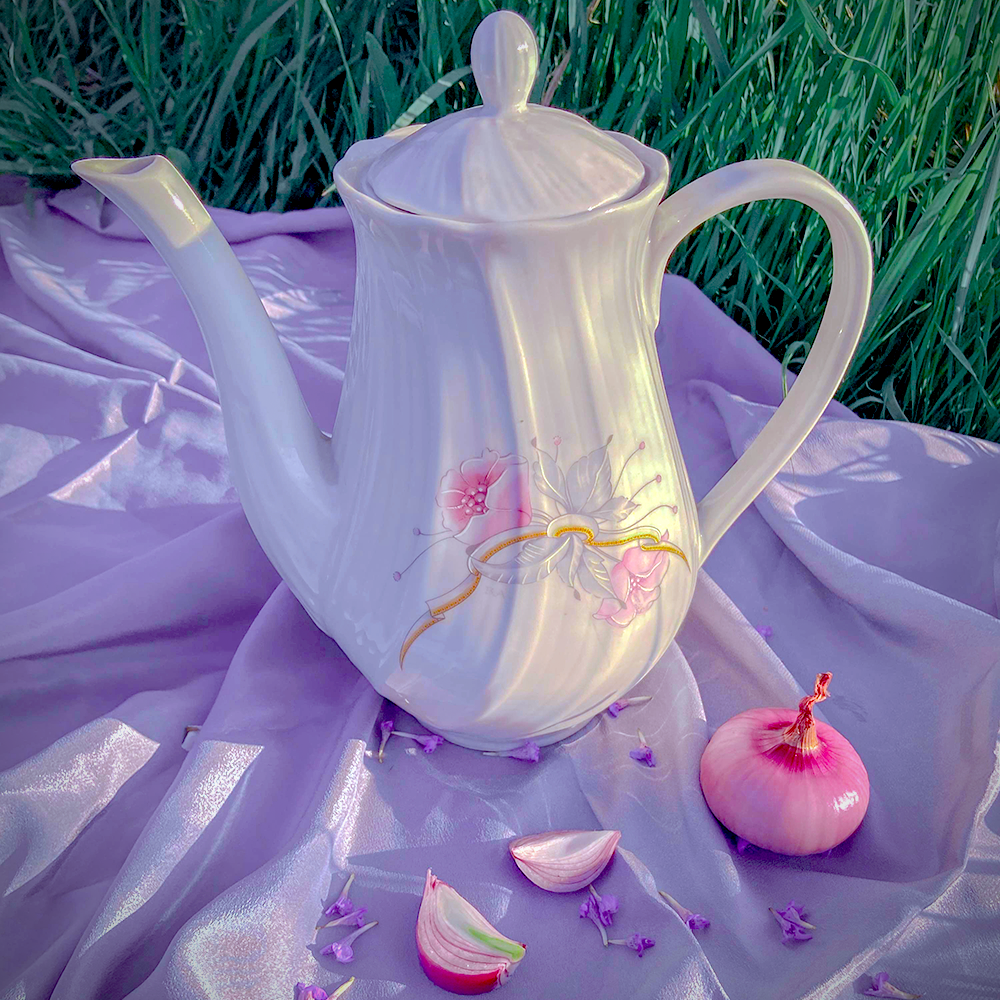
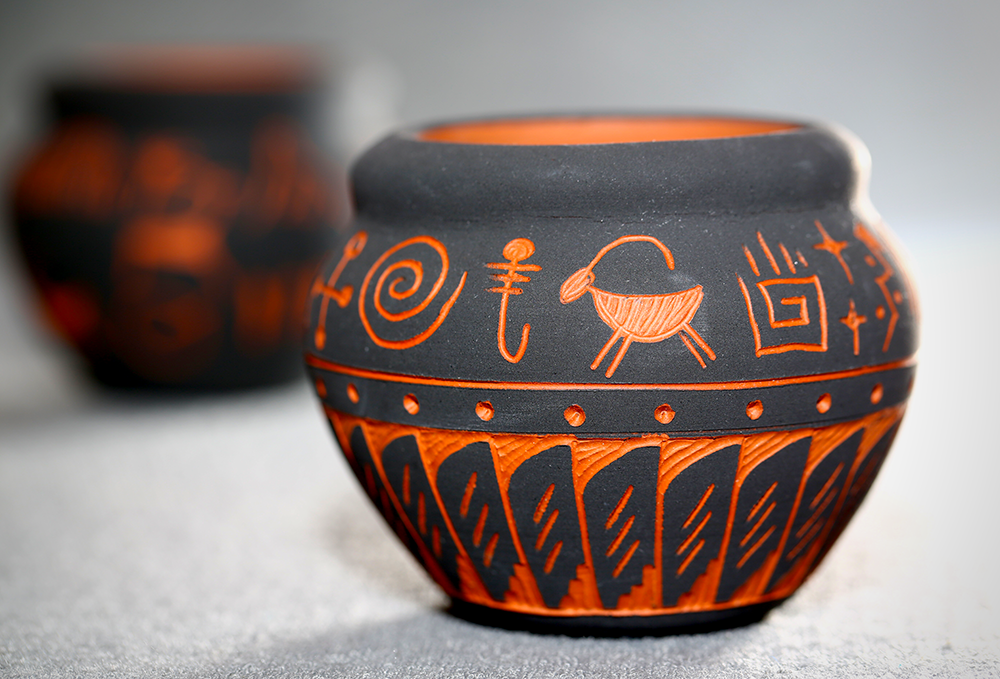
Want to learn more about glazes? Check out KaransPotsAndGlass's video!
Love working with clay?
Check out some of our other ceramic articles:
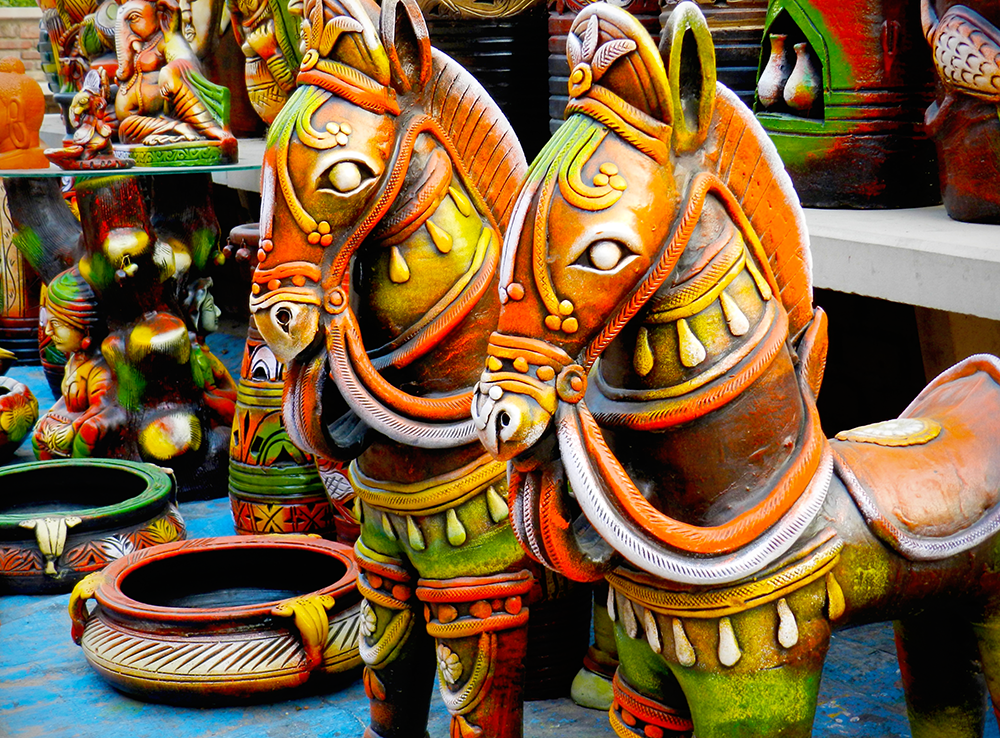
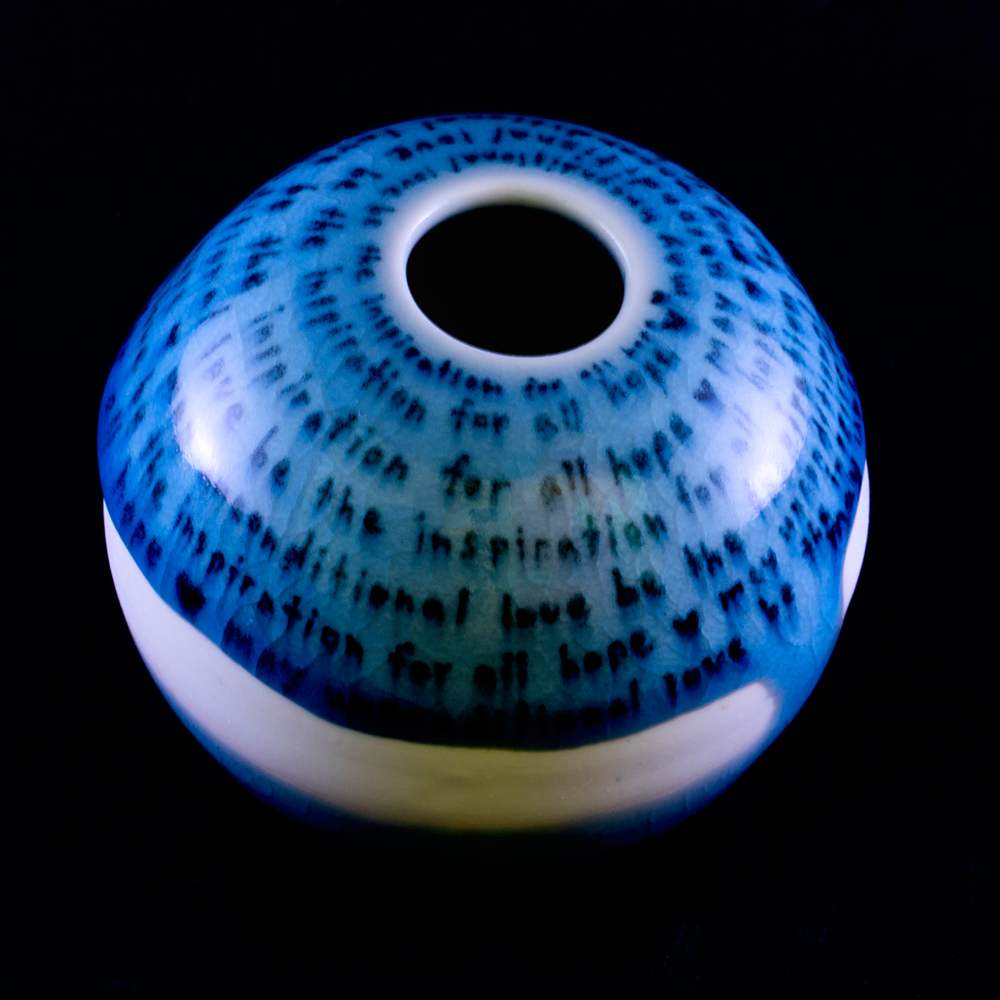
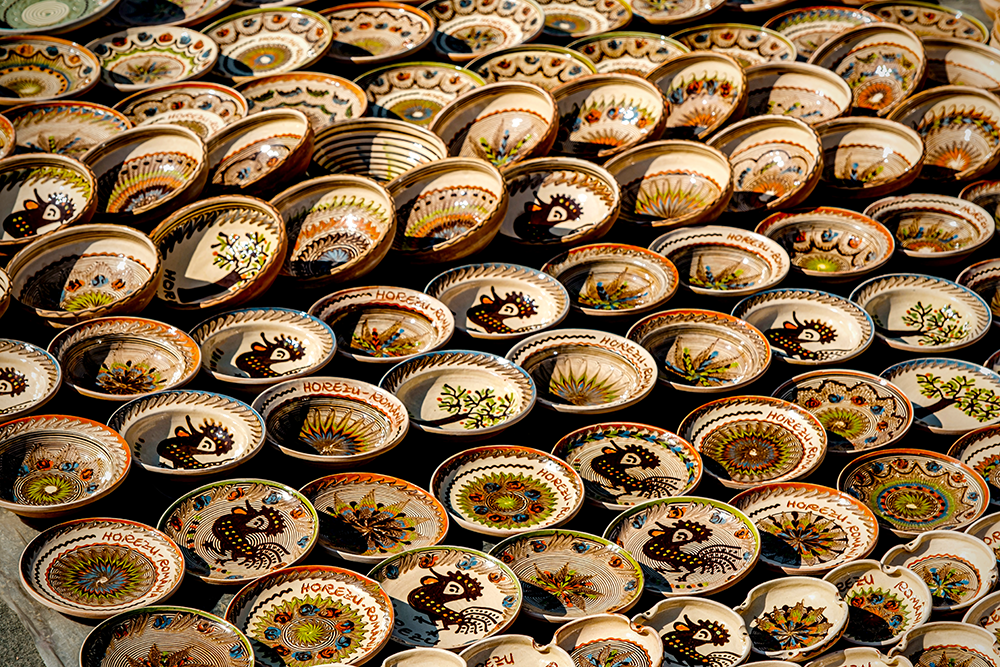